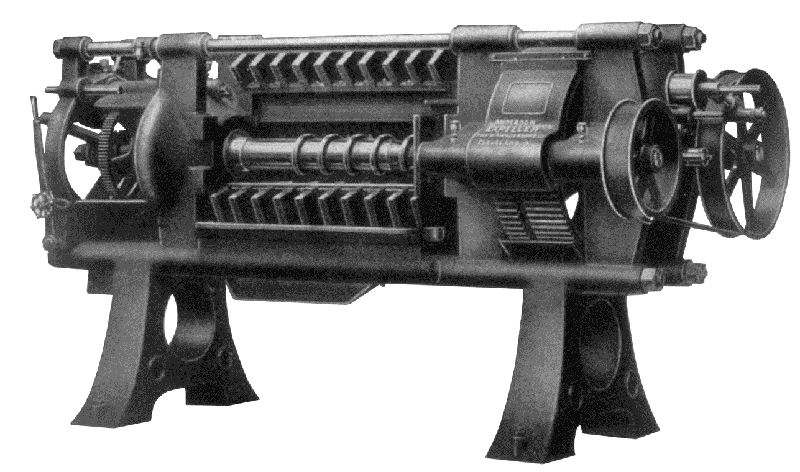
When Valerius D. Anderson filed a patent for his mechanical screw press in April 1900, during the Industrial Revolution, he planted the seeds for a groundbreaking invention that would revolutionize the industry.
At that time, a batch hydraulic press was the only way to mechanically extract liquid from solid material. It could take hours to process a hundred pounds of product this way—slowly squeezing one batch at a time, letting the oil drain out, and then cleaning the extraction basket after each load. It was a lengthy, tedious, and expensive process, and Anderson knew there had to be a better way.
After working in factories since the age of 7 and inventing several other machines throughout his early manufacturing career, Anderson moved to Cleveland in 1880. In 1888, he established his company, V.D. Anderson & Sons, where he invented the first continuous screw press by placing a rotating screw inside a perforated barrel to continuously compress product through the extraction chamber while draining the liquid from the solid material. By making the process practically automatic, Anderson engineered the press to extract oil more efficiently than ever.
Pioneering this process wasn’t without hurdles, though. Here are some of the challenges Anderson had to overcome to design a screw press built to last centuries and how his inventive solutions still set the Anderson Oil Expeller® apart today.
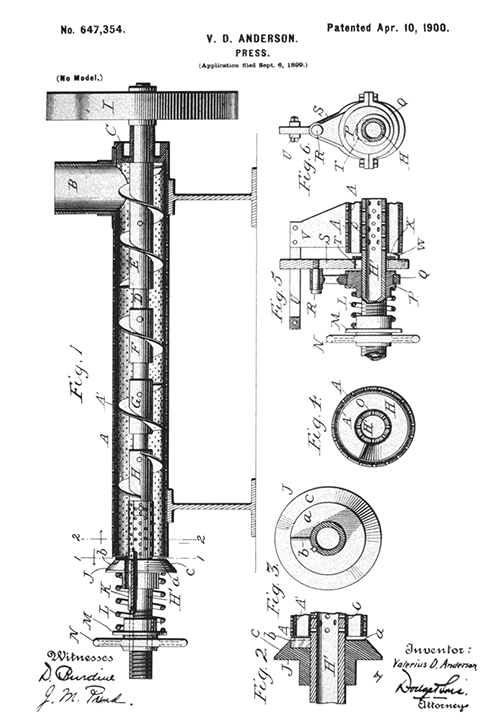
Also read: Debunking the Debate Between Expeller Pressed versus Cold Pressed Oil
Innovating through obstacles
Anderson’s early versions of the continuous screw press employed a continuous screw—a screw with uninterrupted blades, or “flighting,” wrapped around the entire shaft. However, he soon realized that continuous screws generated such extreme amounts of pressure that the drainage surface couldn’t support the load, and the resulting extraction yields suffered.
Think of wringing out a wet rag. No matter how tightly you squeeze the rag with a single twist, you’ll only expel a certain amount of moisture—unless you release the tension, let the liquid redistribute, and then wring it out again to release even more water with each squeeze.
Anderson applied this principle to his screw press design by adding interruptions to the flighting wrapped around the shaft. These interruptions created a pressure gradient of high- and low-pressure zones inside the barrel, allowing the press to efficiently squeeze, release, and squeeze the material again even harder, improving the machine’s ability to extract oil.
But the interruptions in the screw created new problems. Material tended to stall inside these spaces because nothing pushed it forward, hindering the press capacity. To keep material moving through the barrel, Anderson added protrusions called “knife bars” to these interruptions to help promote flow.
Yet another challenge was supporting the immense pressure exerted on the drainage surface. Because Anderson’s screw press generated so much mechanical force to squeeze out liquids from the solid material, standard screens were not strong enough to stand up to the challenge. To answer this dilemma, Anderson designed a drainage cage consisting of rectangular barrel bars arranged with tiny gaps between them, as small as five-thousandths of an inch apart. These drainage bars, specifically engineered to precise tolerances, allowed oil to flow out of the barrel efficiently.
Setting the screw press standard
Since Anderson’s revolutionary invention, other manufacturers have answered with their versions of the continuous screw press based on his original design. As competition for this equipment has increased around the world over the last 123 years, Anderson’s Expeller remains an industry leader for several key reasons.
- Precision: Anderson machines its parts to a much tighter tolerance than other screw press manufacturers, which means that the geometries are more precise, and the parts are more uniform. Although these tight tolerances are more expensive to manufacture, our clients get more consistent performance from our equipment as a result.
- Durability: Anderson also uses higher-quality steel than most screw press manufacturers, which contributes to the durability of our equipment. Our steel is hardened to 60-65 on the Rockwell hardness scale, while other companies use steel only hardened to 50-55 Rockwell — which means our parts last longer, leading to fewer repairs and less downtime. In fact, Anderson equipment installations from the 1920s are still in operation today, thanks to this durable construction.
By using higher quality steel precisely machined to tighter tolerances, Anderson built his screw press to outlast the competition, setting the industry standard for this now ubiquitous machine.
Also read: Pressure Leaf Filter vs. Decanter Centrifuge: Which Oil Filtration System is the Best?
Leaving a lasting impact
Originally designed for rendering animal fat in the meat packing industry, Anderson’s screw press ultimately revolutionized a multitude of industries by transforming extraction from a batch process to a continuous operation. In the years that followed his invention, Anderson’s expeller was modified to process more than 80 different types of fat-bearing materials—catapulting the company to become a world leader in oil extraction.
Anderson’s original screw press quickly expanded beyond animal fat rendering. Within five years of its invention, the machine found a valuable application in oilseed extraction, which has become the main focus of Anderson International Corp. since then.
With a few modifications, the Expeller press gained new applications as a cooking device for grain proteins and starches. Originally known as the Expander-Extruder-Cooker™, this offshoot proved useful for producing pet food, pig and poultry feed, fish food, and even extruded snacks for human consumption. Meanwhile, the dewatering capabilities of the screw press also evolved into other industries like synthetic rubber processing, paper recycling, and much more.
By empowering plants to switch from batch to continuous processing, Anderson’s invention introduced processors to new operational efficiencies and cost savings — making food, fuel, and other forms of fat far more affordable. Still the cleanest and most sustainable way to extract oil, the screw press remains a vitally important piece of industrial equipment throughout the modern food chain, providing the backbone for a number of industrial processes that consumers around the world rely on every day.
As we continue to innovate and improve our solutions, based on more than a century of experience extracting nearly every type of oil imaginable, we keep building on our founder’s legacy to provide the most efficient and economical extraction equipment on the market.
Ready to add more than a century of extraction expertise to your operation? Contact Anderson International today to learn how we can help.