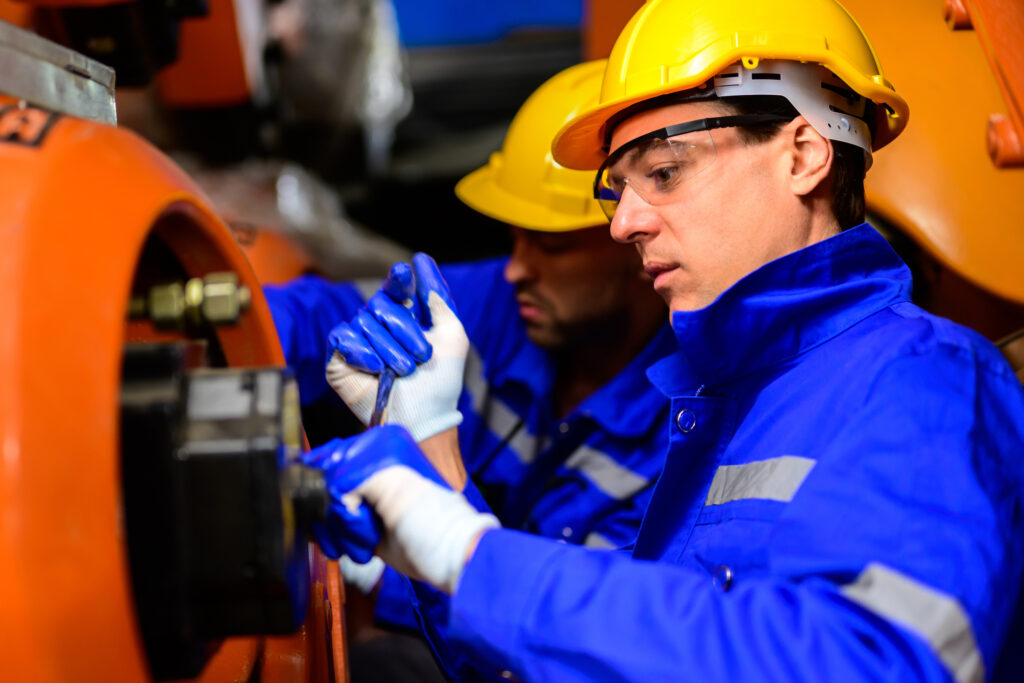
In light of all the recent growth and opportunity we see on the oilseed processing horizon, we here at Anderson International continue to add new resources to better support our client oil mills and processors around the world.
Some of these precious resources, like our brilliant team of engineers who develop innovative new products, have always been part of Anderson’s competitive advantage. These dependable experts aren’t going anywhere. But now, we’re bolstering our troops beyond the supportive staff you already rely on to keep your mill running—giving you a deeper bench of oilseed processing support to help your oil mill improve, evolve, and grow.
Here’s a quick rundown of the support staff and other internal resources available to Anderson International clients.
Reliable account managers from our outside sales team
Each client in North America receives a direct account manager at Anderson, who serves as the primary go-to contact for everything related to their oilseed processing system. International clients outside North America work with one of our international sales agents to fill this role. Wherever you’re located, your account manager should be your first call to help you access any other support or service you need from Anderson.
Internal support from our inside sales team
Of course, there’s a team of people working behind the scenes from our office to support your account manager in the field. This inside sales team is dedicated to quoting and tracking spare part order to keep our clients’ machines running. Although you may never meet them, this team serves a vital role in supplying the parts you need when you need them.
Smooth integration from our project management team
When a client orders brand-new oilseed processing equipment from Anderson International, a project manager ensures the installation goes smoothly. The project manager coordinates on-time delivery of the new capital equipment to the client’s site, and then helps integrate each machine into their operations.
Technical expertise from our service team
Regular maintenance is critical when operating an oilseed processing plant, and Anderson’s service team is committed to keeping equipment up and running. Our skilled service technicians travel worldwide to help our customers with mechanical issues, equipment maintenance, troubleshooting, and rebuilds to ensure minimal downtime and maximum production.
Process problem-solving from our applications engineer
Our applications engineer, the newest addition to the Anderson International team, is the pinnacle process expert on oilseed processing systems. While our service team focuses on mechanical maintenance and routine rebuilds, the applications engineer diagnoses highly technical production issues by analyzing a plant’s entire setup. Our applications engineer can design an effective solution if clients want to upgrade or expand their processing systems, add a new seed cleaning or dehulling system, improve their oil clarification process, or increase overall oil yields.
Also read: The Evolution of Conditioning Oilseeds Before Pressing
Piloting innovative ideas at our new test facility
Oilseed processors are always looking ahead—exploring new products, processes, and ideas to expand their operations. We want to support our clients every step of the way, so we’re excited to announce the opening of our partner’s new test facility in Mexico. The facility is a fully functional mechanical and solvent extraction plant where we can experiment to perfect our offerings. Now that it’s up and running, this test facility will give our customers a launchpad for testing new products and ideas.
Also read: Maximizing Profits with More Energy Efficient Oil Mills
Oilseed processing resources
From our skilled engineers to our service techs and sales reps, the entire team at Anderson International is committed to our customers’ processing success. We partner with our clients every step of the way, from the initial sizing of your new oilseed processing system to installation, maintenance, troubleshooting, and ultimately expanding and optimizing your oil plant as you grow.
Whatever you need to improve your mill, call your account manager to get the ball rolling. And if you don’t have an account manager at Anderson yet, we’d love to have you join the family.
Contact our team today with any questions or inquiries about optimizing your oil extraction operation.