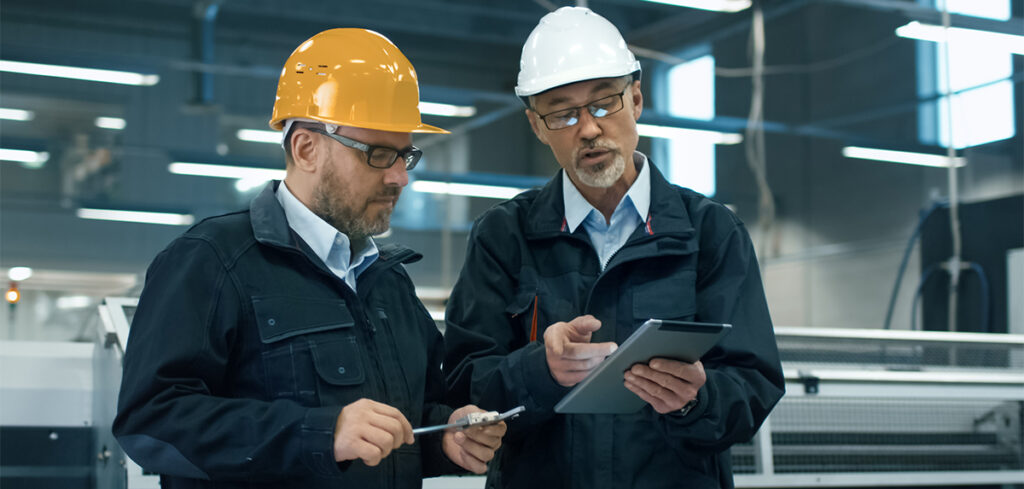
Designing a complete processing system for oilseed is a lengthy and complex undertaking. System layout must allow each unit to operate in unison, and the engineering team must have the foresight to plan for future maintenance and growth. Moreover, the design process can become even more complicated with a hybrid model integrating machines from multiple manufacturers.
This complexity is why processors often turn to manufacturers like Anderson International to tap into their expertise and system integration knowledge. Processing specialists know the industry from start to finish and can provide solutions from new plant layout to improving efficiency years into a facility’s lifetime.
By working with processing experts, oilseed plant personnel can avoid mistakes resulting in costly downtime. Let’s examine what this means for a typical oilseed processing facility.
The scope of a complete processing system
An oilseed processing system design is complicated and must coordinate the various steps of machines during different process stages.
- Storage. Silos and storage facilities protect raw materials and provide access for continual output.
- Grain cleaning and screening. Screener cleaners, aspiration, magnets, and de-stoners remove foreign material and eliminate unwanted material from the oilseed.
- Size reduction. Roller mills, cracking and flaking, grinders, and vertical or horizontal hammer mills reduce the oilseeds’ size upstream for easier oil removal during separation.
- Heat treatment. Steam-jacketed vessels, high-shear extruders, roasters, hot air belt dryers, plate heat exchanges, and expanders apply heat to rupture the oil-bearing structures of the oilseed and deactivate harmful anti-nutritional factors.
- Oil Recovery. Expellers and extractors separate the oil from the seed through mechanical force or the use of solvents.
- Oil Clarification. Decanters and centrifuges, pressure leaf filters, and settling tanks remove solid impurities from the oil product.
- Cake cooling and grinding. Counterflow coolers, belt coolers, and hammer mills cool and grind the meal for safe and easy storage.
- Material handling. Drag and screw conveyors, bucket elevators, and pneumatic conveying systems transport the material.
Coordinating these steps with the correct machines and sizes for the intended use can be a heavy burden for staff at any facility. Whether setting up the initial layout or rectifying inefficiencies down the road, a processing expert will advise on the complete processing system rather than an individual machine or function.
Download the brochure: Oilseed Processing Systems from Design to Delivery
Assess, design, & build
Anderson processing specialists start with an in-depth assessment of a facility’s specific needs, including intended oilseed(s) for processing and output volume. They work with facility personnel to determine layout and ensure it is conducive to maintenance and proper tooling, foresight that can save processors extended downtime in the future.
Based on the processor’s specific needs, Anderson specialists will assist with equipment selection. Whether a processor has selected an Expeller, Expander, or Extruder, the Anderson team is knowledgeable about all compatible upstream and downstream equipment and can supply the complete processing system. By collaborating with Anderson processing specialists, facility personnel ensure every piece of equipment is appropriate, adaptable, and adequately sized for the application.
Once the layout and equipment are approved, an Anderson project manager takes over to procure materials and oversee manufacturing and shipping. The process typically takes 20-30 weeks, and Anderson experts provide continual updates to the processor.
Need assistance with your oilseed equipment now?
Do not hesitate to call us at 1(800) 336-4730 or use our contact form.
Installation & after
Installation generally takes 16-24 weeks, with site preparation overlapping procurement and manufacturing timelines. During install, the Anderson team will work directly with contractors to ensure the setup goes smoothly.
After installation, Anderson’s work doesn’t stop. Several weeks of onsite training and education from process experts ensure plant personnel understand the most effective and efficient ways to operate each piece of equipment as it relates to the complete processing system. The Anderson team stays engaged with the client for the lifetime of the machinery, bringing onsite technical support for troubleshooting or when an operator has changing needs from their systems.
One ongoing service proven beneficial to clients is Anderson’s process audits. These audits evaluate every operating step in a system to compare how a machine should be running versus how it is actually running. The audit can identify where issues are occurring or where inefficiency is causing unsuspecting processors a loss in profit.
Take the example of an Anderson client in Papua New Guinea. The client was struggling with poor press performance when processing local copra. During a visit to the plant, Anderson processing specialists learned that the plant received its copra from various farmers across the island. The copra ranged from 5-20% moisture depending on where it originated. The plant’s drying system, however, was designed to handle material only up to 10% moisture. For the bulk of incoming copra, the client was not sufficiently drying the material, reducing the press’s efficiency. Anderson identified the issue and worked with the processor to install an additional drying step for any product above 10% moisture while allowing for material below 10% moisture to bypass this step and move through the normal process.
Many issues identified in Anderson’s processing audit stem from processors unknowingly veering off the proper sequence of operations in their plant. For example, Anderson experts have worked with several clients drying and sending their oilseed to storage rather than integrating the drying step into their processing sequence. The operator then needs to reheat the seeds when processing begins, wasting time and energy in duplicating the heating step. Other processors use the wrong equipment in their sequence, like when an Anderson specialist discovered a client using a hammer mill instead of a cracking roll to grind product before sending it to an extruder. The hammer mill created too fine of particles for the extruder to operate efficiently.
The list of issues every processing specialist encounters and remediates at sites is long. Often problems occur when facility staff sets up their processing system alone without understanding the importance of process flow and the order of operations. And sometimes staff turnover or lack of training can send an otherwise functioning facility off course quickly.
Anderson’s experience
Anderson’s knowledge of the intricate details and nuances of the oilseed processing industry is an indispensable resource for our clients at any stage in building, troubleshooting, or maintaining a processing system. Every Anderson specialist has several years of operations experience, first-hand knowledge in the field, and an understanding of what it takes to make a facility profitable.
Finally, as an ISO-certified manufacturer, Anderson International stands by its products and provides complete process support spanning a system’s lifetime.
To learn more about Anderson’s processing solutions, contact us today.