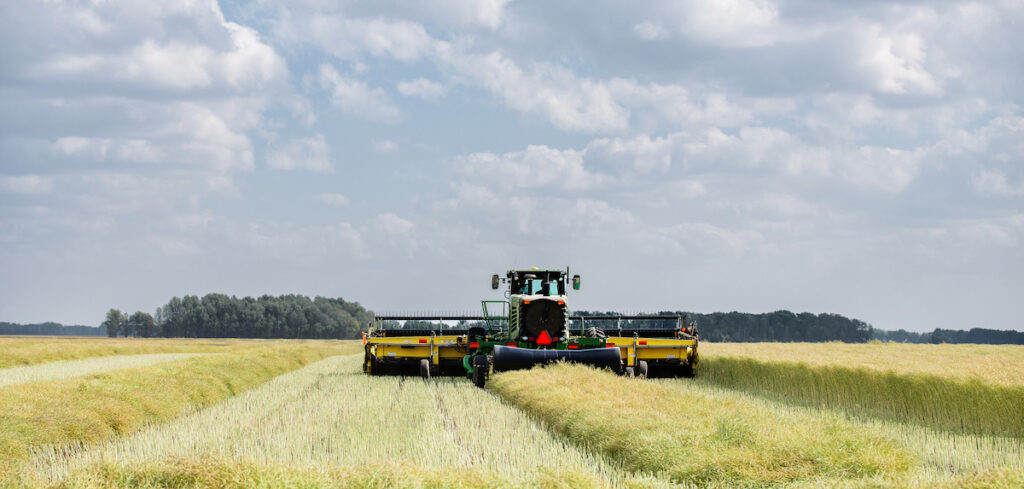
To be effective when processing with an expeller, operators must monitor and adjust several variables. A new batch of material or a different seed type will inevitably respond differently than the last. Everything from the storage of the raw seeds, upstream preparation, and wear on machine parts can impact the expeller-pressed oil process results and efficiency.
Operators know that efficiency saves time, and time is money, which is why it surprises us when we visit a plant and see systems that don’t have an overflow process set up. In most cases, cutting this extra process is an attempt to make do with the bare bones and reduce machinery and costs. What oilseed manufacturers don’t realize is that skipping the overflow process results in lost production, costing the facility much more over time than the initial investment in overflow equipment.
Overflow ensures your expeller-pressed oil process is efficient, saving both time and money required to increase profitability of your processing plant.
The expeller-pressed oil process
An expeller press, or screw press, uses mechanical force to extract oil from the seed. The machine uses continuous pressure and friction from the screw drive to compress the material as it moves through the barrel. Oil drains through barrel spacings and is funneled downstream to clarification. Solids release at the discharge as press cakes and move along a conveyor to cooling and grinding. The expeller-pressed oil process can reduce oil residuals in the meal to approximately five percent.
To reduce residual oil to the smallest amount, operators must run their press at sufficient pressure to compress the material and release the oil. Pressure generation relies on the machine receiving enough material – its rated capacity – feeding at a constant rate.
An expeller receiving a material flow below its rated capacity will not generate enough pressure to squeeze the oil sufficiently from the seed. This situation results in higher amounts of residual oil in the meal, often 10 percent or more left behind. Operating a press in this manner is inefficient and means the processor is throwing away profits by not extracting the maximum amount of oil.
Even worse is when an operator feeds too much material into an expeller for its rated capacity and clogs the press, resulting in costly downtime for repairs.
A typical processing plant will have two to ten expellers onsite to meet production needs. In this setup, operators have to figure out how to make a highly variable material flow at a constant rate to multiple machines. For processors managing multiple expellers, they can maximize their process and opportunity for increased profits with overflow.
Read more about how to avoid downtime with spare parts and with proper plant layout and maintenance.
Need assistance with your oilseed equipment now?
Do not hesitate to call us at 1(800) 336-4730 or use our contact form.
Overflow increases efficiency
A system with multiple expellers uses the main conveyor to transport material to the feed conveyor of each press. It is simple enough to measure the material flow so that the first press or presses receive enough material to meet the rated capacity. The challenge is keeping a constant flow of material at the rated capacity of the last press.
An expeller pressed oil processing system without overflow will feed each expeller at a constant rate, with the conveyer ending at the last expeller in line. The last expeller receives whatever amount of material is left over from previous expellers in the process. Most processors will underestimate the amount of material needed to prevent the final expeller from receiving too much material and jamming. As a result, the last press receives less material than rated capacity and will not compress the oilseed enough to reduce oil residuals to their lowest levels.
A system setup with overflow will feed every expeller first, with the conveyor ending at a recycle bin. Each machine receives enough material for efficient pressing, and then any remaining material flows into the recycle bin. The overflow material will cycle back to the first press for processing in a continuous loop.
One of the system benefits is the level indicator on the recycle bin, which lets the operator know the amount of material inside. If the bin is nearing capacity, the indicator will signal the need to turn down the overall feed rate. A low bin level reading prompts the operator to pick up the feed rate and ensure the last machine is not underfed.
Systems designed with an extruder placed before the expeller should also use an overflow process to maximize feed rate. By doing so, expeller presses and extruders receive the optimal feed rate for their capacity, allowing for efficient oil recovery. Otherwise, processors risk their production quantity and increase operating costs.
Read more about system efficiency: Sequence of Operations is Critical for Oilseed Processing
Complete Processing System Design
With most of today’s processing plants running 24/7, it is more important than ever for oilseed companies to design their systems for maximum efficiency and minimal downtime. Designing complete and efficient systems can be a challenge for even the best processors. Support from a team with the experience and expertise setting up complete processing systems can provide lasting value to processors for the lifetime of their facility.
Anderson International has a team of specialists providing worldwide support at any stage from design to delivery and throughout the lifetime of a machine. Every Anderson specialist has several years of operations experience, first-hand knowledge in the field, and an understanding of what it takes to make a facility efficient and profitable.
Contact Anderson International today to speak with an expert about your complete processing system design.