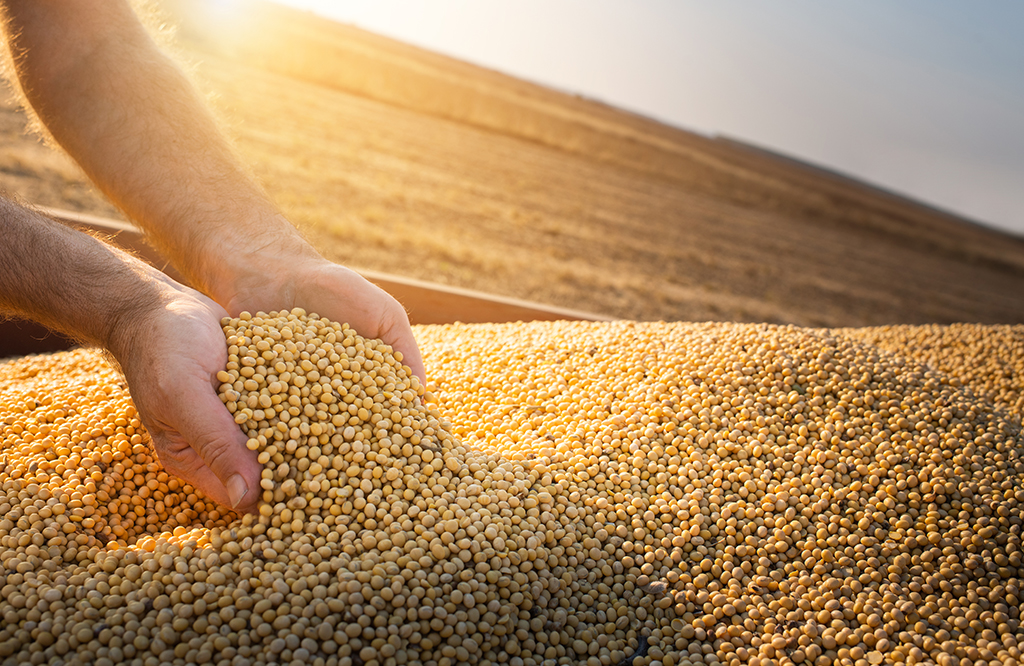
Sticks and stones may not break your bones, but they can certainly wreak havoc on an oil seed processing plant. No matter what material you process or which market you serve, the quality of the seeds you crush determines the quality of the oil and other byproducts. Foreign objects can impede this process and degrade your products, so oil seed cleaning is a crucial first step to remove these contaminants and impurities to ensure you’re feeding your press with only the best material.
Your approach to cleaning seeds can make or break the rest of your operation—impacting your oil’s yield, quality, and value, which filters into your profits and losses. In fact, skipping this critical step could add tens of thousands of dollars to your operating costs and diminish your returns.
Let’s take a closer look at why cleaning is critical in oil seed processing, how it impacts the economics of your operation, and which cleaning solutions can minimize your losses and maximize your profits.
Why oil seed cleaning is so important
When seeds arrive at an oil mill, they typically contain all sorts of foreign material picked up during harvest or transport. This might include:
- Organic impurities: stems, leaves, and grass.
- Inorganic impurities: dirt, sand, stone, and metal.
- Oily impurities: pests, diseases, and weed seeds.
While a top-grade oil seed shipment might only contain about 1% of these impurities by weight, lower-grade seeds might have 5 to 10%. Even the smallest percentage of trash can be detrimental to an oil seed processing operation in several significant ways:
- Degrading oil quality with off-colors, flavors, smells, and sediments
- Absorbing oil during processing, reducing total oil yields
- Diluting the protein content of the press cake, reducing the value of the meal
- Accelerating wear and tear on processing equipment, requiring additional maintenance or repairs
- Wasting electrical energy to process junk material that doesn’t turn any profit
It may not seem like a big deal to run some sticks and stones through the expeller press along with your seeds. But imagine the inconvenience and potential expense of shutting down the entire processing line to fix equipment damaged by rocks or other abrasive materials. These costs can quickly add up, making oil seed cleaning imperative to an operation’s success.
Also read: Extend your Crushing Capabilities with Toll Processing
The cost of dirty oil seeds
Just how much can unclean seeds cost your operation? Consider a typical oil mill that processes 300 tons of soybean per day. At that capacity, a facility will have 1,400 connected horsepower running an Anderson Oil Expeller® and Dox™ Extruder (compared to 2,000 HP per day using similar equipment from other manufacturers).
The electricity needed to power this plant can be measured in kilowatt-hours. At roughly .75 kilowatts per mechanical unit of horsepower, that converts to 1050 kilowatts:
1400 HP x .75 kW/HP = 1050 kW
Most processing facilities run 8,000 hours a year on average (24 hours a day for at least 330 days). With an average industrial electricity cost of about 10 cents per kilowatt-hour, we can estimate that this plant pays about $840,000 per year in electricity bills:
1050 kW x 8,000 hours/year x $0.10 per kW-hr = $840,000
If just 1% of the material they’re pressing is trash, they’re wasting 1% of those energy expenses—that’s $8,400—just to move garbage through the processing line. If they’re using lower quality seeds with 5% foreign material, they’re wasting five times as much—$42,000 a year—just to power the machines to move material that’s not making any money.
This calculation doesn’t even factor in the cost of added wear on the equipment from abrasive sand or stones clanking around inside the machines. It doesn’t account for the lower price of meal with decreased protein content, the loss of oil absorbed by these impurities, or the oil’s diminished quality.
Once you factor in all these costs, dirty oil seeds can cut into your bottom line. Removing all that trash can instantly recover significant losses. Most oil seed cleaning systems will show a return on investment within two years of operation, saving processors tens of thousands of dollars annually.
Common oil seed cleaning solutions
There’s a wide range of methods used for cleaning oil seeds. The exact steps and systems vary significantly from one seed to another, and even from one facility to the next. An oil mill that handles peanuts (which grow underground) needs an efficient way to remove stones and rocks from their seed. Meanwhile, a plant processing copra from tropical locations must clean off sand before making coconut oil.
In general, oil seed cleaning machines and methods work by separating foreign materials from seeds based on size, weight, density, or other properties. The most common seed-cleaning solutions include:
- By size: Vibrating shaker screens use varying hole sizes to sieve oversized and undersized materials away from oil seeds.
- By weight: Fans blow air through the seed material to pull out lightweight materials like dust and sand in a process called “winnowing” or “aspiration.”
- By density: Gravity tables, called destoners, separate small stones that are the same size and weight as the oil seeds.
- By magnetic force: Magnetic separators grab bits of metal or ferrous material, like bolts that may have fallen off the combine during harvest.
Most seed cleaning systems combine several of these methods into one system—for example, leveraging screens to separate material by size and blowers to separate by weight. Some facilities add extra steps to their oil seed cleaning process, like a final dust removal, to further improve the quality of their seed material before pressing.
Achieving cleaner oil seeds
Building the right cleaning practices into your process from the start ensures optimal products and profits at the other end. But choosing the right seed cleaning equipment and knowing how to integrate these seed cleaners into your overall processing system isn’t as simple as it sounds.
The oil seed experts at Anderson International have designed, manufactured, and commissioned processing equipment installations in more than 1,000 plants worldwide. We can help optimize your entire operation, from oil seed cleaning to oil pressing and every step in between, to ensure that your process is set up to yield the best quality products and the maximum possible profits.
Contact Anderson to learn how cleaner seeds can boost your bottom line.