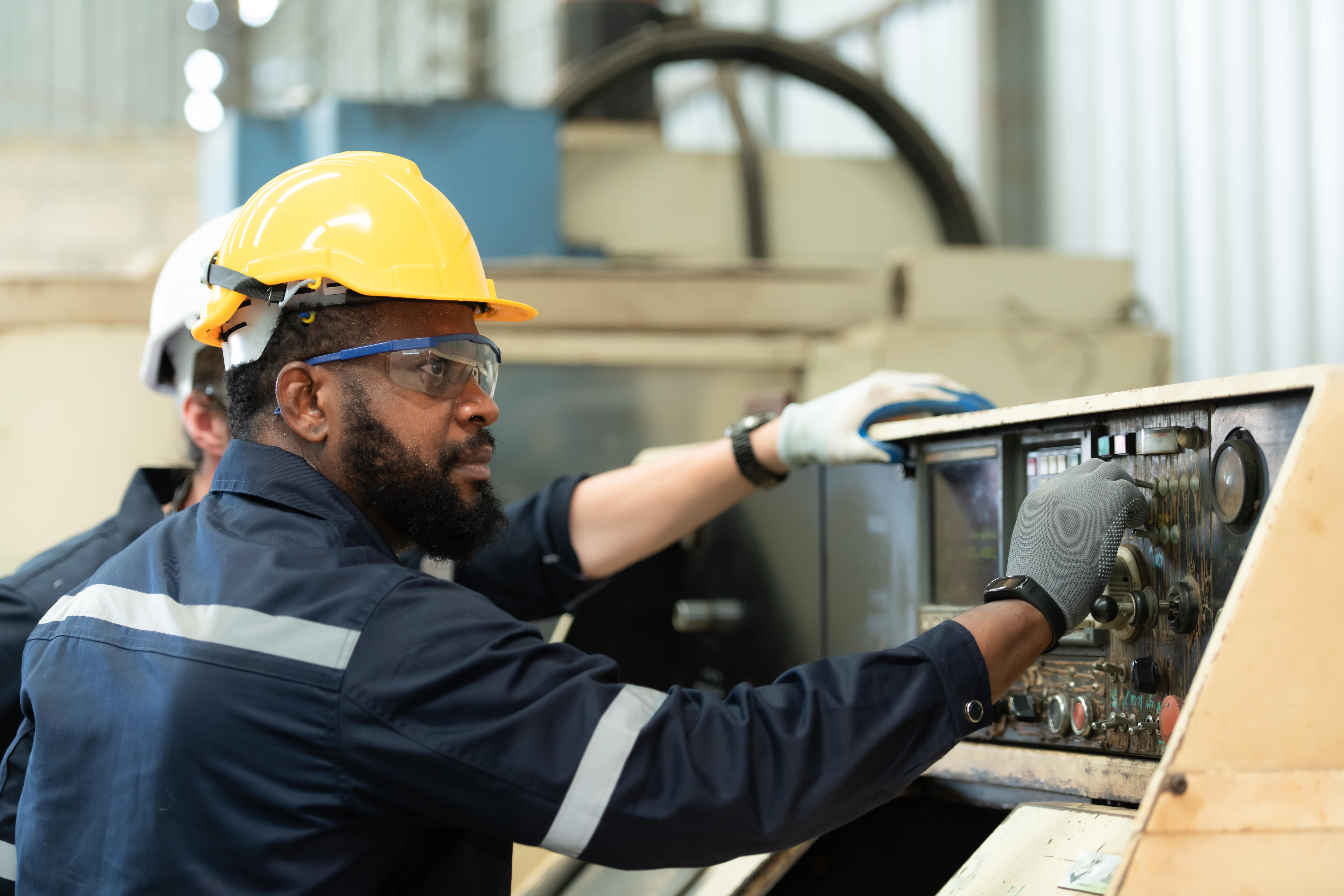
In an industrial oilseed processing plant, where heavy-duty extraction equipment is constantly enduring wear and tear from crushing tough material, optimal performance depends on regular service and equipment maintenance. Just as you routinely take your car to the shop for a check-up every 10,000 miles, it’s even more important to schedule preventative maintenance to examine the health of your press. In line with our goal to keep our customers up and running, Anderson International is committed to providing end-to-end support, from on-site service calls to more intensive repairs and rebuilds.
Driven by the success of our customers, we’re continuing to bolster our service offerings for equipment maintenance to keep plants crushing. With experience servicing more than 12,000 units operating in over 1,000 plants in more than 100 countries around the world, our technicians have unmatched expertise in analyzing, maintaining, and optimizing oilseed operations of every size and market niche.
Now, we’re ramping up our world-class service to make it more convenient than ever for plants to get the professional support they need.
Help is just a service call away
To deliver the robust maintenance support that our oilseed processing clients demand, we’re reinforcing our field service team, which now consists of five dedicated service technicians. These highly skilled techs are focused on doing on-site service calls for customers running Anderson’s extraction equipment, including our oil expellers, extruders, and expanders.
A service call with Anderson’s techs includes a thorough tear-down and inspection of your machines, using specialized tooling like thermal imaging and vibration sensors to assess the health of the equipment. The best time to schedule an on-site service call is during your planned biannual maintenance shutdown, which allows our techs to safely examine every piece of extraction equipment. Plan to have each machine offline for at least 48 hours for proper inspection, and if you’re servicing multiple machines, you’ll want to allow for multiple days of downtime.
Ideally, you should schedule a service call with Anderson at least a month before your equipment maintenance shutdown to ensure the availability of parts and personnel. To fully prepare for your service call, you should also have the following items on hand:
- Spare wearing parts, in case we need to replace any components during inspection
- Equipment manuals and complete maintenance records
- Personal protective equipment (PPE) or safety training required for our techs
If you need help identifying the normal wearing components for your machine or can’t locate your original equipment manuals, contact Anderson for guidance. The sooner you start making arrangements for your next planned shutdown, the smoother it will go.
Expanded service routes
As our service team grows, we’re also launching expanded service routes in the continental U.S. to make equipment maintenance even more convenient for our customers. Initially, these service routes will cover locations within 600 miles (approximately a 10-hour drive) from Anderson’s headquarters in Stow, Ohio, outside of Akron. Customers along these service routes, which repeat quarterly, can take advantage of free pick-up and drop-off of parts and rebuilds.
For example, when you order spare parts for a piece of extraction equipment, this service route offers free delivery of your replacements. Likewise, if your on-site inspection reveals that a specific component needs to be rebuilt, the service route can pick up your worn component for free. Bring it back to Anderson’s shop for a complete machine rebuild, leveraging our specialized in-house tooling, and then drop off the rebuilt component at no extra charge.
Contact Anderson to learn more about these service routes or to schedule an equipment rebuild that coincides with your local pick-up schedule.
Additional services
In addition to our expanding service routes and growing team of technicians dedicated to performing service calls, we still offer the same reliable aftermarket services that set Anderson apart in the industry. These include:
- Operational training to help our clients make the best use of our extraction equipment. Our technicians develop standard operating procedures (SOPs) for each system and educate processors on how to properly operate our oil expellers, expanders, and extruders.
- Equipment maintenance training to show customers how to extend the life of their extraction equipment with proper upkeep. This training walks your team through a typical inspection, teaching them how to repair and rebuild machines if they break down.
- Process audits to examine your plant’s efficiency. Our process engineers evaluate your entire system to identify inefficiencies and other opportunities for improvement, looking beyond the equipment to optimize your upstream seed treatment and overall sequence of operations.
Of course, our skilled technicians aren’t limited to service calls only during planned downtime. If your equipment breaks down unexpectedly or you need help troubleshooting the root cause of a strange noise or an unexplained drop in oil recovery rates, our techs will come as soon as possible to solve your processing problems. Leveraging video conferencing technology, we may even be able to offer virtual training and support to serve clients around the globe in real time—no travel required.
Schedule your equipment maintenance now!
Unplanned downtime is detrimental to any oilseed processing plant. Every minute your machines sit idle eats away at the bottom line—which means every minute wasted trying to service a machine yourself, rather than turning to the experts at Anderson, can add up to a costly mistake. Proactive, planned maintenance is critical to avoiding unexpected breakdowns and preventable repairs. The sooner you start planning your next shutdown—and scheduling a service call from Anderson to coincide with it—the smoother your maintenance turnaround will go.
At Anderson International, we’ve been committed to keeping our extraction equipment running at peak performance for more than 130 years, with equipment from the early 1900s still in operation today. By tapping into Anderson’s industry-leading knowledge, proactive processors can leverage our deep expertise to keep oil – and profits – flowing smoothly.
Contact Anderson today to schedule a service call from our dependable expert technicians.