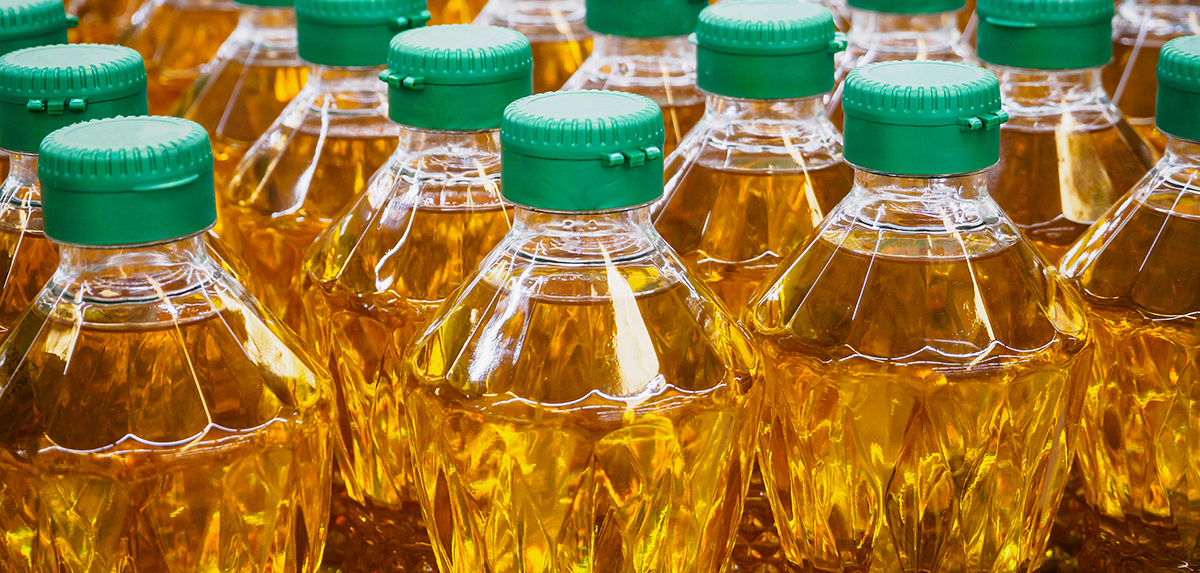
Dox delivers extrusion system flexibility
Soybean products are among a few food sources containing all eight amino acids. And since soy is a complete protein, soybeans are one of the most vital sources of vegetable protein and edible oil. Additionally, soybean meal is an essential protein source used for poultry and livestock around the world.
However, soybeans contain anti-nutritional factors, such as trypsin inhibitors and urease enzymes, that must be deactivated by heat treatment to make the soybean suitable for consumption by humans and livestock. There are multiple options available for processors and their customers to take advantage of the highly nutritious nature of soybeans.
Traditional cooking versus high-shear extrusion
The most common methods for processing soybeans are solvent extraction and mechanical extraction with a screw press. Each process has its benefits. The mechanical process is often selected for its simplicity of operation, low CAPEX and OPEX for preparation and recovery, and versatility in processing other grains and complete feed.
When processing soybeans using a screw press, like the Anderson Expeller®, manufacturers must take specific steps before the expelling process to increase the machine’s throughput and efficiency. The traditional oilseed preparation process uses multiple machines to shear, flake, cook, and dry the oilseeds. Typically, this includes energy-draining equipment like steam batch cooking vessels and dryers.
An alternative to traditional preparations involves using a high-shear dry extruder like the Anderson Dox™ Extruder. Dry extrusion uses mechanical energy to shear, cook, and dry soybeans without an external heating element or steam. It removes the need for multiple machines, reduces machine footprint in a facility, and is particularly beneficial for small-scale processing operations where steam sources may not be affordable or readily available. In addition to the increased efficiency and reduction of energy costs, dry extrusion is beneficial in that the cooking method maximizes the qualities of protein and energy in the soybean. Dry extrusion results in full-energy soybeans because all of the original fat is present. Full-energy soybeans have the advantage of being a good source of protein and a great source of metabolizable energy from the oil.
Read more: Dry extrusion cuts costs and adds capacity for oilseed processors.
How the Dox™ extruder works
In an Anderson Dox extruder, raw soybeans are fed into the hopper and conveyed through the barrel by a rotating screw. The mechanical force creates a high-pressure and high-temperature environment to break down the oilseed cellular structure, releasing the oil trapped within. At this stage, high oil-containing materials may have oil drained through an optional drainage cage. This oil is funneled to join the oil exiting the expeller and moving to the screening tank.
At the end of the barrel, a choke apparatus forces the product through an adjustable ring opening of decreasing diameter to generate a high-shear environment per the Venturi effect. The increase in shear forces against the choke surface area helps tear apart the cell structure further to release the oil.
The product will reach its maximum temperature at the choke, up to 160°C (320°F), resulting in a rapid phase change of water from liquid to gas at the machine’s discharge. As the water transitions from liquid to gas, it escapes from the extruded product, driving down the material’s moisture content to under 6%. The high pressure and temperature created by the extruder destroy harmful substances and microorganisms. Additionally, due to the short cooking time, around 30 seconds, extrusion minimizes the protein’s degradation within the oilseed. The material can then be fed into the expeller for oil recovery with increased efficiency.
Need assistance with your oilseed equipment now?
Do not hesitate to call us at 1(800) 336-4730 or use our contact form.
Extreme flexibility
Unlike wet extruders or other dry extruders on the market, the high-shear Dox design allows for more flexibility in a processing plant. The Dox can accommodate variations in seed type and oil content, offering versatility to the facility, and the design also can extend the time between maintenance and improve safety.
The Dox has adjustable clearances on the choke to account for variations in oilseed sizes. Adjusting the discharge clearanceensures the right size cone cross-sectional area to shear different sized products properly. This change requires about half-hour downtime and allows for both the production of higher-end, lower throughput products made with more expensive raw materials and low-density, lower-cost materials.
To allow for different types of oilseeds, the Dox is the only extruder on the market to date that has an option to add a drainage cage. Seeds like sunflower, coconut, palm kernel, and canola range from 40-60%oil by weight. When you subject these products to friction and high pressure, the seeds will release significantly more oil than a lower oil density seed such as soybean. This amount of oil can flood the machine to the point that it will not function. The drainage cage allows excess free oil to drain off so the extruder can efficiently break down the cell structure and mechanically cook the seed.
The design of the shaft and the ram also improves extrusion flexibility. Unlike a fixed setup of other dry extruders, the Dox bullet choke can be adjusted while the machine runs to close in against the product and add more backpressure. By adding this backpressure, a processor can better control the amount of heat generation and pressure inside the extruder. As internal components inevitably start to wear over time, higher pressure can make up for the wear, extending the periods between maintenance and prolonging the machine’s life. Additionally, when a machine goes down, the pressure maintained inside can be a safety issue for unaware processors. The adjustable choke on the Dox allows pressure to be released from the machine before maintenance. On a fixed-choke extruder, the only way to release pressure is by opening it up. If the pressure built up inside the machine releases too quickly, it can cause an accident or a blow-up. An adjustable choke is not offered in all dry extruders and is one of the notable safety features of the Dox.
The Anderson difference
When setting up or expanding an oilseed processing facility, the benefits of adding high-shear dry extrusion with a machine like the Dox are clear. Installing a Dox ahead of an expeller doubles the press’s capacity, replaces energy-consuming heated cooking vessels, and doubles the life of pressing parts. The Dox is engineered to add extreme flexibility to your process, far outpacing other wet or dry extruders on the market today. For more information about the Dox Extruder, contact our Anderson International team.