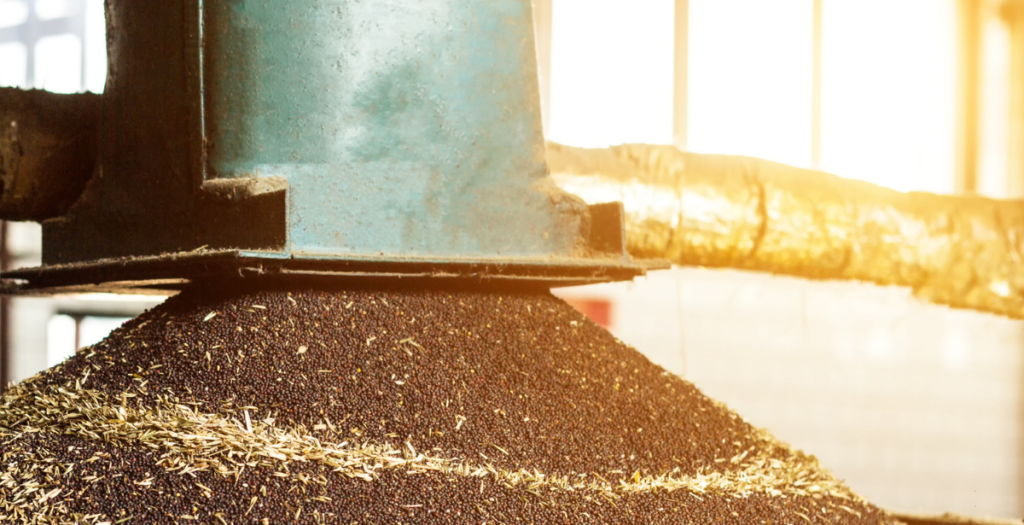
Soybeans are the world’s most dominant source of vegetable oil, with more than 370 million metric tons being processed this year—more than the other six highest-volume oilseeds combined. Since solvent extraction is the most commonly used method of extracting vegetable oil, it makes sense that most of the world’s solvent extraction equipment is designed specifically for handling soybeans, which contain about 16-20% oil by weight. But if you want to process other oilseeds with higher fat concentrations in this same extraction equipment, it requires an additional step of processing before proceeding to the extractor..
What is pre-pressing?
Pre-pressing refers to the process of running high-fat oilseeds through a mechanical expeller press before sending the material to a solvent extractor. After the oilseeds have been cleaned, flaked, cooked, and dried, a worm shaft propels the material through a screw press inside a perforated barrel. The press gently squeezes the flaked material to release oil, draining through tiny perforations in the barrel.
As opposed to a full-press system, which thoroughly crushes oilseeds to squeeze out as much oil as possible, leaving about 6-8% residual oil in the cake, a pre-press runs faster and compresses the seeds less aggressively, leaving about 16-20% residual oil for the solvent to extract downstream. Technically, any expeller press can be converted to a pre-press by simply increasing the speed of the worm shaft, which reduces the pressing force.
Pre-pressing combines the best of both systems: the pre-press removes higher percentages of oil that are easier to physically squeeze out of the solids, while the solvent extractor leverages chemicals to separate the remaining hard-to-press oil effectively.
Also read: Understanding Hexane Extraction of Vegetable Oils
Why is pre-pressing necessary?
If you feed high-fat seeds like canola (40% oil by weight) into the same extractor you use to process soybeans (20% oil by weight), the extractor speed would need to be reduced enough to allow the additional fat sufficient residence time to drain out or the extractor would need to grow in size. Additional solvent would be required to remove the higher level of fat, and the desolventizing steps would require tremendously larger equipment consuming significantly more energy in order to heat the products and solvent hot enough to vaporize off the hexane. When compared with the investment and operating costs of a pre-press, a large solvent system does not make economic sense.
Pre-pressing is critical for processing seeds containing more than 20% oil by weight because it offers a much more economic solution than a large solvent extractor. The resulting de-oiled pre-press cake, as it’s called, will behave more like soybean in the solvent extractor because the fat concentration is now similar to soybean.
In lieu of pre-pressing, the other (far more expensive) option would be to design specialized extractors dedicated to each type of seed, depending on its oil content. You’d need one kind of extractor for oilseeds like canola/rapeseed that contain 40% oil by weight (more than twice as much as soybeans) and another extractor for processing cottonseed, which contains 31-38% oil.
Instead of having separate extractors for every seed, Anderson solved this problem by developing the pre-pressing process so that oil mills could leverage existing soybean solvent extraction equipment to handle seeds with higher oil concentrations simply by adding a pre-pressing step upstream.
Also read: Advancing Solvent Extraction with the Invention of the Expander
Which oilseeds require pre-pressing?
Oilseeds that contain at least 23-25% oil by weight can benefit from pre-pressing to lower the fat content before solvent extraction. Prime candidates for solvent extraction pre-pressing include high-fat oilseeds like:
- Canola/rapeseed (40-45% oil)
- Sunflower (45-64%)
- Peanut (46-56%)
- Cottonseed (31-38%)
- Copra (34%)
- Palm kernel (45-55%
The processing capacity of each plant also factors into the pre-pressing decision. Pre-pressing enables processors to handle high volumes of commodity oilseeds at capacities of up to 1,000 tons per day. However, when it comes to smaller-scale production of specialty oilseeds at lower capacities, many processors depend entirely on full-press mechanical extraction equipment rather than taking on the expenses of solvent extraction. Mechanical processors have no use for pre-pressing—unless they’re double-pressing, in which case, the initial press run could be considered pre-pressing.
Overcoming pre-pressing challenges
Although pre-pressing is essential to prepare high-fat oilseeds for solvent extraction, the de-oiled pre-press cake can also present some challenges for the extractor. This densely compressed cake isn’t ideal for solvent flow because hexane may channel around it instead of permeating it to dissolve the oil completely.
To solve this challenge, Anderson invented the expander in 1966 to transform pre-press cakes into a porous material for more optimal solvent extraction. By using the Anderson Solvex™ Expander between the pre-press and the extractor, processors can improve efficiency, minimize operating costs, and maximize their oil recovery, leaving less than 1% residual oil after extraction.
Since pioneering solvent extraction pre-pressing and inventing the Solvex Expander, Anderson has continued to revolutionize the extraction process by innovating new solutions. Regardless of which high-fat oilseed you’re processing or which extraction system you use, Anderson’s extraction experts can provide the expertise and support to help optimize your operations.
Contact Anderson to troubleshoot your solvent extraction pre-pressing process, or download our guide to learn more about maximizing oil recovery from pre-press cakes.