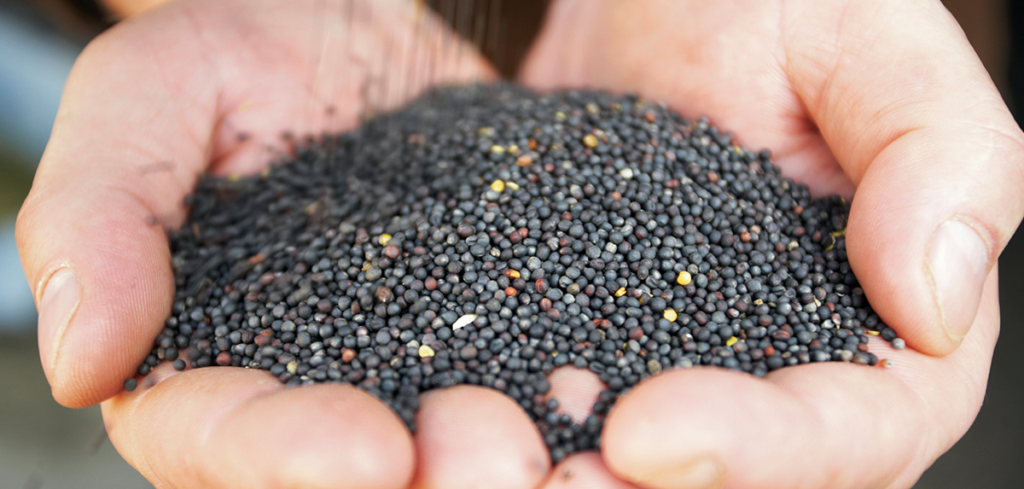
Although canola oil is a common ingredient today in grocery stores, restaurants, and home kitchens, the popular commodity has a relatively short history compared to other oilseeds. Since canola oil first hit the market in the 1970s, canola processing has quickly advanced as crop varieties and pressing methods have evolved.
However, canola’s genetic predecessor—rapeseed—has been cultivated for millennia, long before plant breeders isolated the traits that made natural rapeseed oil undesirable. Rapeseed processing, like canola processing, has improved over time to enhance the quality of the end products, making canola more valuable for a variety of different applications today.
Origins of global canola processing
Taking its name from the Latin word for turnip (rapum), the rapeseed plant is closely related to turnips, cabbage, cauliflower, kale, and mustard. Like most members of the mustard family, rapeseed contains high levels of erucic acid and glucosinolate—which have historically limited the end-use applications of this crop.
As early as the 13th century, rapeseed processing in Europe produced oil both for cooking and lighting oil lamps. When steam power came around, rapeseed oil found new industrial uses because it could bind to steam-washed surfaces better than other lubricants due to its high erucic acid levels.
During World War II, the demand for rapeseed oil-based lubricants soared due to its use on marine engines in naval and merchant ships. With oil supplies from Europe and Asia blockaded, Canada faced a critical shortage of rapeseed oil and began ramping up production to become the leading world supplier it is today.
By the 1950s, people were beginning to question the nutritional aspects of rapeseed. High levels of erucic acid and glucosinolates gave the byproducts a pungent taste and odor. While not harmful for human consumption, high levels of glucosinolate proved potentially dangerous for other animals. So, plant researchers set out to reduce these undesirable components, making the oil more nutritional and palatable for humans and animals both.
In 1974, Canadian researchers at the University of Manitoba bred several varieties of rapeseed to produce a cultivar low in both erucic acid and glucosinolates. They named this new variety “canola,” short for Canadian oil with low acid.
Canola processing methods
Rapeseed and canola seeds contain up to 45% oil by weight, which is approximately twice as much oil as soybeans. These tiny, round, black seeds form inside of long, slender pods called siliques.
The tiny size and round shape of the rapeseed can make canola processing difficult, because the seeds tend to roll around inside machines and avoid compression points in screw presses. An important preparation step in processing canola is flaking the seeds to break up their round structure, making them easier to convey and process through the downstream equipment.
At that point, processors may use several different methods to process canola seed into oil and meal.
Traditional mechanical pressing
Traditionally, flaked canola is moved through stacked cooking and heating vessels to steam-heat the material, releasing the oil inside, hardening the structure, and reducing the moisture level for optimal extraction. Then, the dried flakes enter a screw press or oil expeller like the Anderson Super Duo™ Series Expeller®, which mechanically crushes the oil from the seeds.
Read more about the Super Duo’s role in pressing other difficult-to-process crops.
Solvent extraction
Today, solvent extraction is one of the most popular methods of processing canola oil. Due to its high oil content, canola must be pre-pressed down to 16-20% oil by weight before being fed to the solvent extractor. Pre-pressing allows high oil content material like canola and sunflower to be processed in a solvent extractor, which is only suitable for material like soy with 20% fat or less by weight. From the pre-press the product can be further processed into collets using an Anderson Solvex™ Expander or sent directly to the extractor after being cooled to 60°C (140°F) to avoid vaporizing hexane in the extractor. By soaking the pre-press cake or collets in hexane, processors chemically separate the oil from the solids, leaving less than 1% residuals behind. Both the oil and the meal must be carefully processed further to remove any remaining chemicals, which can be toxic.
Due to the high expense of solvent extraction, this method is best for large-capacity plants that process more than 1,000 tons of oilseed per day.
Canola oil extrusion
Now, canola oil processors looking for more efficient, cost-effective methods are turning to high-shear extrusion instead. Whereas traditional mechanical presses often required a series of expensive, energy-draining equipment upstream to separately shear, cook, and dry the seeds, an extruder like the Anderson Dox™ Extruder combines all these processes in a single machine. The Dox Extruder shears, cooks, and dries seeds quickly without relying on expensive steam-heated cooking vessels or harmful chemicals.
Instead, by creating a high temperature, high pressure, high shear environment, the Extruder breaks down the canola seeds to release the oil for more efficient pressing. An extrusion system like the Dox can double the capacity of the expeller press while reducing oil residuals to 5%. An extruder makes the expeller’s work even easier, which can increase the wear life of the pressing parts as well. Unlike other extruders, Anderson offers an optional drainage cage to allow for direct extrusion of high oil content materials like canola and sunflower. Without a drainage cage, other extruder suppliers require the materials to be pre-pressed prior to extrusion, adding additional, costly processing steps that the Anderson high shear extrusion system does not require.
Making canola products
After extraction, crude canola oil is filtered and clarified to remove any remaining solids and unwanted colors, tastes, or odors. Most refined canola oil is consumed as cooking oil, although it has many non-food uses as well, such as industrial lubricants, paints, lacquers, soaps, and cosmetics. Driven by the search for more renewable energy, canola oil is also showing promise as a source for biodiesel fuel.
Meanwhile, the solid meal that remains after extraction is cooked again to drive off the hexane from the meal and ground to produce a protein-rich ingredient for animal feed. In mechanical extraction, the meal does not have to be cooked further to remove solvent from the meal, resulting in higher protein quality. Additionally, the solvent recovery process is unable to recover 100% of the solvent from the meal. Residual hexane, a known carcinogen, is still present in the solvent extracted meal. In mechanical processing, there is zero risk of chemical exposure or contamination in the finished product.
More efficient canola processing
Although canola’s high oil content makes it a valuable commodity, it also makes it difficult to process compared to seeds that contain less oil. For example, an oil processor in Pennsylvania recently tried to run canola through the extruder they use to process soybeans. Because canola seeds contain twice as much oil as soybeans, the excess oil quickly clogged their machines. They had to shut down production to clean up the oily mess.
To process this oil-rich seed more effectively, the facility installed the Anderson Dox Extruder. As the only extrusion system on the market with an optional oil drainage cage, the Dox handles excess oil from canola, coconut, sunflower, and palm kernel more efficiently than other machines.
The Anderson Extruder also offers longer wear life than competitors’ machines that use inferior materials. While operating competing extruders, the customer was replacing parts every six or eight weeks—whereas the Dox only requires replacement parts every 26 weeks or so. Similarly, the Extruder lengthens the life of expeller pressing parts from 22-24 weeks to 48-52 weeks or longer.
Building on decades of specialty oilseed processing experience, Anderson International provides the expertise and the equipment that processors need to be profitable in canola processing, rapeseed processing, and other growing oilseed markets.
To learn more about pressing canola seed efficiently with less mess, contact an Anderson International expert today.