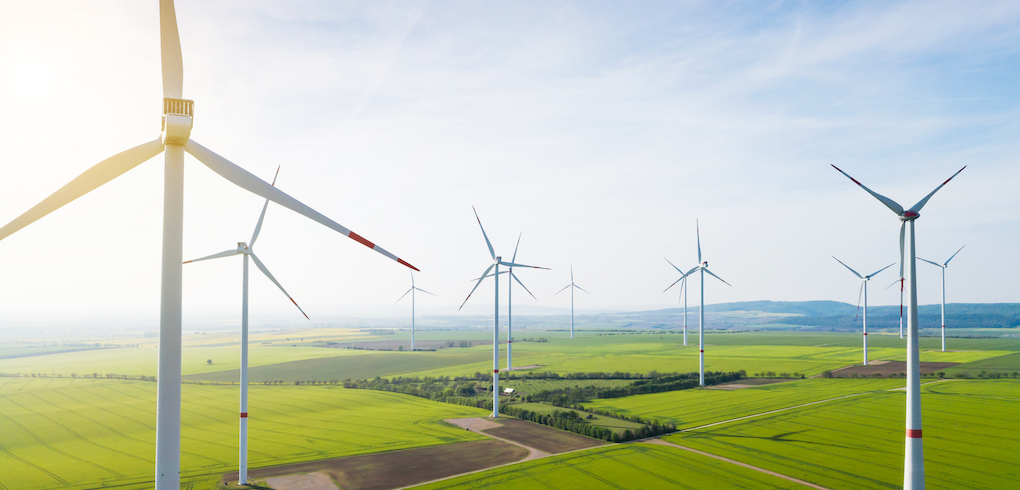
In the past few years, mechanical oil processing plants have been slowly but steadily increasing their average processing threshold. Just five years ago, the idea of a 500 ton-per-day (TPD) mechanical plant would have sounded crazy, but today, it’s not uncommon to see processors pursuing larger-scale plants to stay competitive.
While large-scale processing plants have historically relied on solvents like hexane for processing, the attitudes toward this method are shifting. The U.S. Environmental Protection Agency labeled hexane as an atmospheric pollutant and the environmental impact and safety concerns surrounding solvents are pushing more plants toward safer, more sustainable mechanical processing alternatives.
Adopting more efficient machinery
Traditional mechanical oil processing plant layouts include multiple machines that separately shear, flake, cook, and dry the seeds to extract the oil. These processes often use energy-draining equipment like steam batch cooking vessels and dryers.
These machines can be expensive to operate and maintain, and the risk of downtime can incapacitate processors and create inconsistent end products. This method often requires prolonged heat exposure on the material, up to 15 or 20 minutes. This extended heat exposure puts the oil and proteins in the seeds at elevated risk of damage, potentially degrading the quality of the end products.
Instead, more processing plants are turning to a high-shear extrusion system for their processing needs.
Read More: Extrusion Technology Crucial for the Plant Protein Market
Lower capital expenditures
Unlike the extensive series of equipment required to prepare oilseeds for pressing in a traditional processing setup, an extruder like the Anderson Dox combines several steps together, so processors can maximize their capital investment in one multi-functional workhorse.
High-shear extrusion eliminates the need for separate flaking mill, steam heating, and drying steps required in stack cooking vessels. The Dox efficiently generates mechanical heat through friction to rupture the cellular structure of the oilseeds, while using pressure and high temperatures to cook the seeds quickly. This process deactivates harmful enzymes in the seeds, while flash-drying excess moisture and cooking the proteins for more efficient oil recovery.
Stack cookers, by comparison, are generally more expensive than extruders—often costing twice as much to achieve similar TPD capacity. By eliminating steam heat, processors also bypass the need for an expensive industrial boiler system, which comes with its own complications, costs, and safety concerns.
By generating mechanical heat more efficiently through friction, the Dox shortens cooking time to approximately 20 to 30 seconds. This rapid cooking process minimizes the potential degradation of protein within the oilseed, promoting more efficient oil recovery leaving less than 6% residuals.
Need assistance with your oilseed equipment now?
Do not hesitate to call us at 1(800) 336-4730 or use our contact form.
Reduced operating expenses
In addition to lower upfront capital costs, an extrusion system also reduces operating and maintenance expenses for processors over time.
Energy consumption is typically one of the biggest operational costs associated with the industrial equipment used in mechanical oil processing. To generate steam heat in a traditional processing plant requires burning some type of fossil fuel or biomass, which inherently releases pollutants. Steam utilities can be expensive items on a processor’s balance sheet—not to mention the environmental impact they leave behind.
Plus, industrial boiler systems also necessitate a certified boiler technician on-staff, while racking up recurring expenses for large-scale water utility usage and water treatment.
An extruder, on the other hand, relies entirely on electrical energy, which can be generated from renewable resources such as wind, hydro, or solar energy. Because they use more sustainable sources of energy, extruders are more cost-effective and more environmentally friendly than steam-based equipment.
Extruders use mechanical energy to generate heat without steam—resulting in lower energy costs per ton compared to traditional processing plants.
When it comes to the environmental concerns surrounding solvent extraction, the Dox Extruder similarly offers several benefits. Unlike solvent extraction, the extruder and press system avoids the use of harmful chemicals for cleaner, safer, energy-conscious processing.
Increased capacity and lifespan
By efficiently combining multiple processes into one machine, the Dox can double the capacity of the downstream screw press—cutting per-pound energy usage in half. After extrusion, a screw press like the Anderson Expeller can release the oil more efficiently, further reducing energy consumption and ultimately extending the equipment’s wear life.
As an added benefit, processors purchasing equipment directly from Anderson have access to the Return Material Authorization program for the machine’s entire lifetime. Anderson’s team of experts will inspect, rebuild, and salvage as many parts as possible when repairing the machine, which can save processors hundreds of thousands of dollars or more over the lifetime of the machine.
When it comes to the equipment maintenance involved in mechanical oil processing, some smaller, compact extruders might require a rebuild every three or four weeks. But thanks to its large size and rugged construction, the Dox Extruder maintains an average rebuild time of about 22 to 24 weeks. With a longer maintenance cycle, this machine delivers greater overall productivity than a multi-machine operation that faces frequent downtime for repairs and rebuilds.
Read more: How to Avoid Expensive Downtime: Plant Layout and Maintenance
Enhanced quality and flexibility
Designed with versatility in mind, the Dox Extruder can accommodate variations in seed type, size, and oil content to make mechanical oil processing plants even more efficient.
Raw oilseeds are fed through the barrel of the extruder by a rotating screw. The mechanical force creates a high-pressure, high-temperature environment that breaks down the cellular structure of the seeds to release the oil trapped inside.
A choke apparatus at the end of the barrel can be adjusted to accommodate different seed sizes, empowering processors to handle new materials without requiring additional equipment. By adjusting the barrel choke to add extra backpressure, processors can better control the heat generation and pressure inside the extruder—effectively making up for natural wear to prolong the machine’s lifetime.
The Anderson Dox is also the only extruder on the market equipped to handle material with more than 30% oil content. Using a proprietary oil drainage cage to capture free-flowing oil that would otherwise clog the equipment, the Dox can effectively process sunflower, canola, coconut, palm kernel, and other high-oil content seeds.
Without a drainage cage, high-oil content material like sunflower seeds would need to be pre-pressed to an 18-20% oil range before it could be extruded and finally pressed down to 6-8%. This added step could add significant costs to the process, making Anderson’s drainage cage a cost-effective addition to a large-scale operation.
Read more: High-Shear Extruder Adds Extreme Flexibility For Soybean Oil Milling
More efficient mechanical oil processing
Installing a Dox Extruder ahead of a screw press expeller gives processors a competitive edge by cutting costs, increasing capacity, and replacing energy-consuming equipment with a more effective solution to oilseed processing.
These benefits are amplified at large-scale facilities, where cost-cutting pressures can be paramount for profits. In most cases, one high-capacity machine is less expensive than three or four smaller ones linked together.
As the largest dry extruder currently on the market, Anderson’s 12-inch Dox Extrusion System can process up to six times higher capacity than competing equipment—making high-capacity oil processors even more efficient and cost-effective.
Contact Anderson International today to see how much money your processing operation can save with a Dox Extruder system.