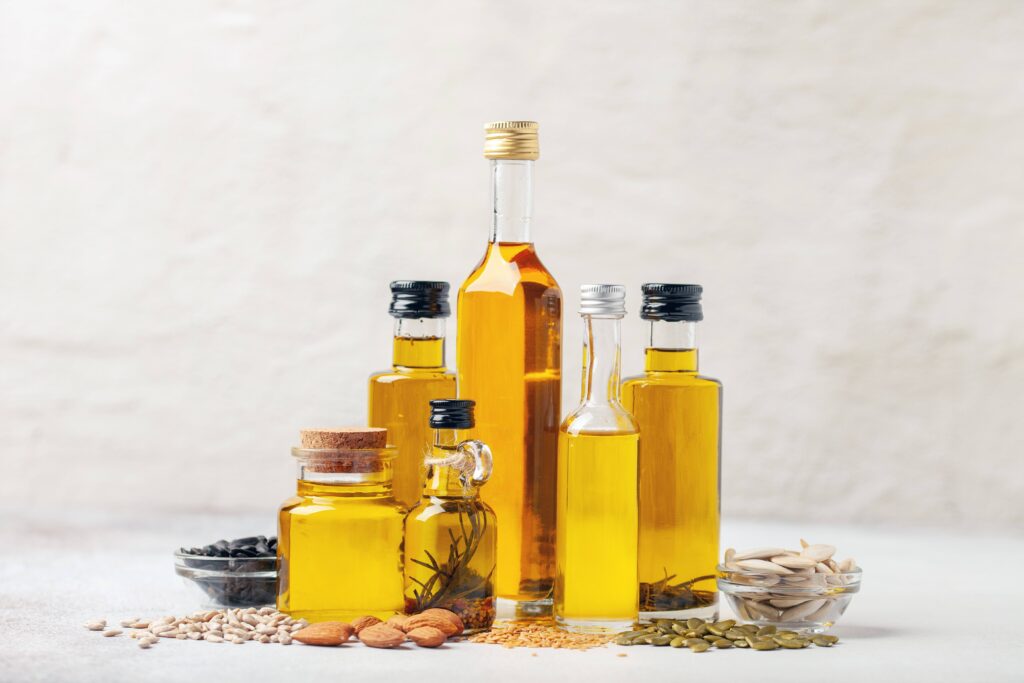
Ever since inventing the first continuous mechanical screw press in 1900, Anderson International has continued innovating new and improved solutions for seed oil extraction. Their monumental press invention sparked a series of other innovations—including the original Expander-Extruder-Cooker (EEC), which led to the development of the Solvex Expander, now used widely to prepare oilseeds for solvent extraction.
But, as valuable as the Expander was (and still is today) as a continuous cooking device, it (like the EEC) relies on steam injection to add moisture. While moisture can be helpful to facilitate heat transfer during the cooking or conditioning process, it’s not ideal because it requires an additional drying step afterward to remove the moisture added during cooking. This is an essential step because oil presses like the Anderson Expeller® operate most efficiently when processing seeds at moisture levels of around 5%.
So, the seed oil extraction engineers at Anderson started looking for a new way to elevate the temperature of oilseeds enough to achieve a thorough cook without adding moisture. Initially, they tried a completely dry extrusion setup to process oilseeds with a screw geometry similar to the Solvex, but without the steam injection, the material did not get hot enough to cook properly.
Also read: The evolution of conditioning oilseeds before pressing
While running without steam, they noticed that the seed material started to exhibit more free oil at the discharge than usual as oil dripped from the solid material leaving the machine. The engineers realized that if they could add additional resistance at the discharge or choke point, the friction could further elevate the temperature, rupturing to cell structure to release the free oil.
This realization led to the invention of the Dox™ Extruder in the 1980s. The Dox (Dry Oilseed eXtruder) was designed to mechanically shear, cook, and dry seed material in a single machine—replacing expensive stacked cooker/dryer installations with a more streamlined solution.
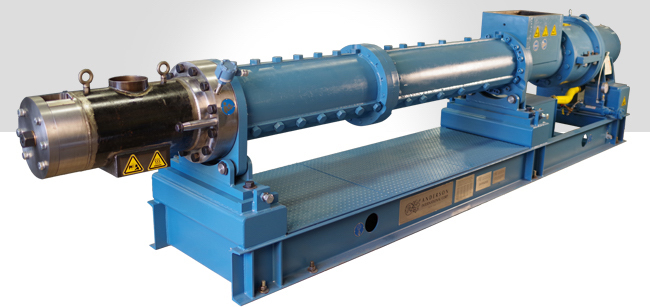
How the Dox™ Extruder works
Similar to the barrel action inside the original Expeller press, a rotating screw conveys seed material through the Dox Extruder—generating a frictional force that creates a high-pressure, high-temperature environment to break down oilseeds. This mechanical heat flash-dries excess moisture and cooks the proteins without external heat or steam. Frictional heat elevates the temperature inside the Extruder above the boiling point of water to achieve simultaneous cooking and drying in a single step.
At the end of the barrel, a choke apparatus forces the material through an adjustable opening of decreasing diameter, generating a high-shear effect based on the Venturi principle. This increase in shear force against the choke surface helps tear the seeds’ cellular structure apart, releasing the oil trapped inside.
By creating such a high degree of shear over such a small surface area of the discharge, the Dox Extruder quickly and effectively cooks the seeds in 20 to 30 seconds—compared to traditional stacked cooker/dryers, which require residence times up to 20 minutes. The seed material reaches a maximum temperature of 160 degrees Celsius (320 degrees Fahrenheit) at the choke of the Extruder, instantly vaporizing the water from liquid to gas at the discharge. This rapid phase change drives the moisture content below 6%, preparing the material for more efficient pressing.
The high pressure and temperature generated inside the Extruder produce enough heat to destroy harmful enzymes and anti-nutritional factors, like urease and trypsin inhibitors in soybean or toxic gossypol in cottonseed. However, the quick cook time saves the seeds from the prolonged heat exposure of traditional stacked cookers, which can potentially scorch the fat and the protein in the seeds, degrading the quality of the end products. Extrusion minimizes this protein degradation to preserve the nutritional qualities of the meal while facilitating more efficient oil recovery downstream.
The benefits of extrusion
The Dox Extruder simplifies upstream processing for seed oil extraction by combining multiple processes into a single step. This multi-functional machine unlocks several critical benefits for oilseed processors:
1. Reduced energy consumption
Because the Extruder generates heat from mechanical friction rather than external heating elements, it operates with a lower energy cost per ton than traditional processing plants that rely on expensive steam heat to power energy-draining stacked cooking and drying vessels. The Dox Extruder consumes 25-30% less energy than the nearest competing extruder, saving processors tens if not hundreds of thousands of dollars each year.
2. Increased press capacity and lifespan
Running an Extruder upstream significantly increases the press operation’s efficiency, doubling the Expeller’s capacity downstream. Extrusion also lengthens the life of the pressing parts more than twofold, extending the average rebuild time of a press from 22-24 weeks without an extruder to 48-52 weeks when paired with an extruder. This decreased downtime ultimately improves a plant’s profitability.
3. Improved product quality
The Extruder’s rapid cooking process destroys toxins and other anti-nutritional factors and cooks proteins without degrading them. Extrusion promotes more efficient oil recovery, with residuals below 6%, and protects the quality of the other byproducts—including chemical-free, Expeller-pressed ECOMEAL, the lowest cost-per-ton soybean meal on the market that performs on par with other competitors in feed formulations.
Optimizing seed oil extraction
Designed to process high-capacity oilseeds while minimizing machinery needs and energy consumption, the Dox Extruder is ideal for high-protein commodity oilseeds like:
These high-production volume seeds can benefit from the extrusion cooking process, which improves digestibility and nutrient availability for animal feed formulations. Currently, the Dox is the only extrusion system on the market that incorporates a drainage cage for oil-rich materials like sunflower, canola, and peanuts. Without the drainage cage, these could otherwise clog standard extraction equipment, adding significant time and costs. The Extruder offers a cleaner, more efficient, and more cost-effective solution for seed oil extraction.
With a long history of manufacturing durable systems for seed oil extraction across industries and applications, Anderson’s engineers have worked on more than 12,000 systems in at least 100 countries around the world. Built to last for decades, Anderson’s extrusion equipment comes with the aftermarket service and extraction expertise needed to keep plants running smoothly by leveraging the benefits of extrusion.
To learn more about efficient seed oil extraction with the High-Shear Dox Extruder, download Anderson’s latest eBook.